Industries Served
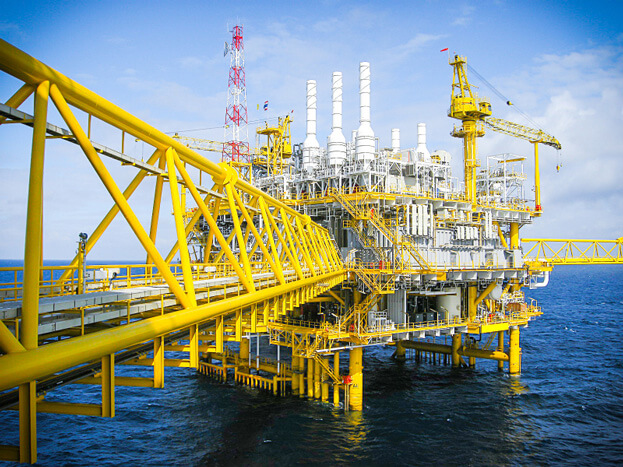
Though oil itself is not corrosive, today’s production occurs in harsh and highly corrosive environments. The challenges for any material of usage include increased depths of wells, tar sands, heavy oils, more sour wells, and arctic and high pressure/high temperature conditions. Today, specialty stainless steels, high nickel alloys, and titanium products are replacing carbon steel and 316L/316 stainless in many applications.
Sandmeyer Steel Company’s stainless steels are excellent choices for topside construction. The life cycle cost benefits are significant.
For blast and firewall 316L/316 has been the material of choice. However, duplex 2304 offers the same resistance to corrosion and buckling while providing a significant weight and cost reduction.
Fire protection is vital on an offshore platform. Historically, copper alloys have been used for this piping system because of their resistance to seawater. Our superaustenitic SSC-6MO and super duplex 2507 are replacing the copper alloys.
In cable trays, stairs, treaded plates, and walkway applications 316L/316 is being replaced by lean duplex LDX-2101®, and 2304.
The flows of many wells are combined through the use of manifolds. The fluids are just as corrosive as the main process piping, and the pressures are high. 2507 is perfect for this service.
On offshore platforms, oil and gas coolers are necessary. Their heat exchangers use seawater as a coolant. These exchangers are often made of 2507 and SSC-6MO.
Gravity separators are used to separate the individual elements of the incoming mixture. Since this environment is just as corrosive as the main process piping, 2205, 2507, and SSC-6MO are specified.
For severe sour gas service, nickel alloys 625 and C-276 are utilized. Nickel alloy 825 finds usage in flow and injection lines.