Industries Served
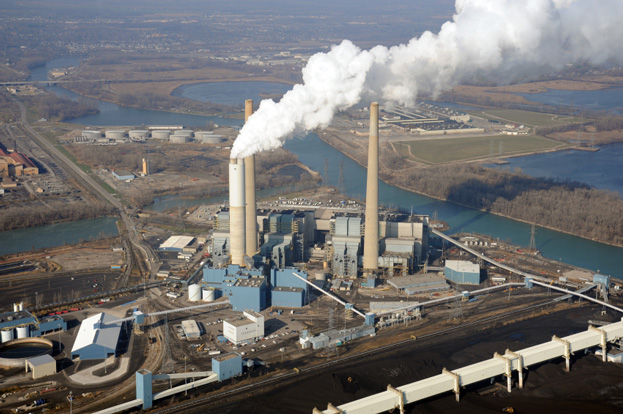
Sandmeyer Steel Company’s stainless steel, nickel alloy plate and titanium products are used extensively throughout the power generation market. Our products can be found in coal-fired and natural gas generation and hydroelectric and geothermal industries served. Other major applications of our products can be found in nuclear power and air pollution control (both covered in their own application section). As new green energy power sources such as wave and tidal are developed, be assured that they will also rely on our products.
Coal-fired boiler systems offer unique alloy challenges. The high temperatures and corrosive gases present often require some of our premier corrosion/heat resistant materials. Our 304L/304, 309S/309H/309, 310S/310H/310, 316L/316, 317L/317, 321H/321, 347H/347, 904L, SSC-6MO, LDX-2101®, 2205, and 2304 are utilized in these systems. Nickel alloys are often used where highly corrosive gases may contain any number of harmful compounds. Alloys 330, 600, 625, 800H/800HT, and C-276 are the most commonly used materials.
Many nickel alloys have been designed to resist the severe temperatures and stress environments encountered in gas turbines. Alloy 625 is often utilized in the fabrication of combustion components, spacers, transition ducts, cases, rings, discs, and exhaust systems.
High strength and heat-resistant stainless steels are also found in land-based gas turbines. The martensitic and precipitation hardening grades 410 and 17-4PH offer high strength and fatigue resistance. Sandmeyer Steel Company’s heat-resistant stainless steels 309S/309H/309, 310S/310H/310, 321H/321, and 347H/347 resist oxidation up to 2000F (1093C) and are standard materials of construction. Alloy 321H/321 is often used for recuperators. Our duplex grades LDX-2101®, and 2205 are replacing austenitic stainless steels where pitting resistance and higher strength are required.
In hydroelectric power generation, dam gates and sluice gates are often made of 304L/304 or 316L/316. Roller guides are often speced with Sandmeyer 17-4PH.
Geothermal energy generation occurs when a naturally occurring mixture of pressurized water and steam is heated underground to between 200 – 325°C. The steam and hot water are drawn up by production wells. The high pressure hot water is separated at a geothermal plant into steam and water. The dry steam is used to power a steam turbine and produce electricity.
Geothermal brines can be very corrosive. They are acidic and can contain many harmful compounds. These corrosive compounds and gases at high temperatures make it necessary to utilize corrosion-resistant materials in the design of process plant equipment. 304L/304, 316L/316, 310S/310H/310, and 321H/321 are the workhorse alloys for the geothermal industry.
When these materials fail or when the corrosive environments cannot be controlled by corrosion inhibitors, duplex grades 2205 and 2507 and superaustenitics 904L and SSC-6MO have performed well. The wide variation in geothermal brines has meant, however, that no one material is the answer to every situation. In the most challenging environments, it may be necessary to use our high performance nickel alloys – 600, 625, 825, and -C276.
Engineering efforts are underway to harness the power of waves and tides. Some prototypes are using stainless steels that have a long track record of resistance to seawater. Duplex alloys 2205 and 2507, with their combination of strength and corrosion resistance, will likely play a key role in this demanding environment.