Placa de Acero Inoxidable
La Compañía Sandmeyer Steel mantiene un inventario completo de placa de acero inoxidable 304H en espesores desde 3/16" hasta 6-1/2" en incrementos de 1/8" listo para entrega inmediata y usarse en sus aplicaciones de alta temperatura.
3/16" | 1/4" | 5/16" | 3/8" | 7/16" | 1/2" | 9/16" | 5/8" | 3/4" | 7/8" | 1" | 1 1/8" |
---|---|---|---|---|---|---|---|---|---|---|---|
4.8mm | 6.3mm | 7.9mm | 9.5mm | 11.1mm | 12.7mm | 14.3mm | 15.9mm | 19mm | 22.2mm | 25.4mm | 28.6mm |
1 1/4" | 1 3/8" | 1 1/2" | 1 5/8" | 1 3/4" | 2" | 2 1/4" | 2 1/2" | 2 3/4" | 3" | 3 1/4" | 3 1/2" |
31.8mm | 34.9mm | 38.1mm | 41.3mm | 44.5mm | 50.8mm | 57.2mm | 63.5mm | 69.9mm | 76.2mm | 82.6mm | 88.9mm |
3 3/4" | 4" | 4 1/4" | 4 1/2" | 4 3/4" | 5" | 5 1/4" | 5 1/2" | 5 3/4" | 6" | ||
95.3mm | 101.6mm | 108mm | 114.3mm | 120.7mm | 127mm | 133.4mm | 139.7mm | 146.1mm | 152.4mm |
La aleación 304H (UNS S30409) de acero inoxidable es una variación de la Aleación 304 austenítica con 18% de cromo y 8% de níquel, en la que el contenido de carbono se controla dentro de un rango de 0.04 a 0.10 para proporcionar una mayor resistencia a las altas temperaturas a las partes expuestas a temperaturas superiores a los 800€ F. Esta aleación puede considerarse para una amplia variedad de aplicaciones y presenta una combinación excelente de resistencia a la corrosión y maquinabilidad.
Especificaciónes: 304H Cromo - Níquel(US S30409)
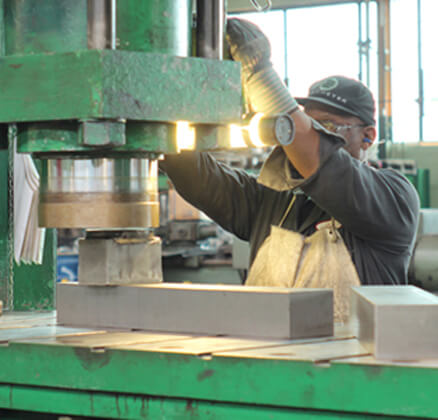
Propiedades Generales
Las Aleaciones 304 (S30400), 304L (S30403), y 304H (S30409) de acero inoxidable son variaciones de la aleación austenítica de 18 % cromo - 8 % níquel , la aleación más conocida y utilizada de la familia de aceros inoxidables. Estas aleaciones pueden considerarse para una gran diversidad de aplicaciones donde una o más de las siguientes propiedades son importantes:
- Resistencia a la corrosión
- Prevención de la contaminación de productos
- Resistencia a la oxidación
- Facilidad en la fabricación
- Excelente formabilidad
- Apariencia estética
- Facilidad de limpieza
- Alta resistencia y bajo peso
- Buena resistencia y estabilidad a temperaturas criogénicas
- Disponibilidad fácil de una gran diversidad de formas de producto
Cada aleación representa una combinación excelente de resistencia a la corrosión y fabricabilidad. Esta combinación de propiedades es la razón del uso extendido de estas aleaciones que prácticamente representan casi la mitad de la producción Total de los Estados Unidos en acero inoxidable. Los aceros inoxidables 18-8, principalmente las Aleaciones 304, 304L, y 304H, están disponibles en una gama amplia de presentaciones de producto incluyendo en lámina, cinta, y placa. Las aleaciones están cubiertas por una diversidad de especificaciones y códigos relacionados con o reguladores de la construcción o uso del equipo fabricado con estas aleaciones para condiciones específicas, por ejemplo: alimentos y bebidas, sanidad, criogenia, y aplicaciones sometidas a presión.
La Aleación 304 es la Aleación estándar puesto que la tecnología AOD ha hecho que sea más fácil y económico obtener niveles de Carbono más bajos. La Aleación 304L se usa para productos soldados que puedan estar expuestos a condiciones que pudieran causar corrosión granular ya en servicio.
La Aleación 304H es una modificación de la Aleación 304 en la cual el contenido de Carbono se controla hasta un rango de 0.04-0.10 para ofrecer una mejorada resistencia a las altas temperaturas en las partes expuestas a temperaturas superiores a 800°F.
Composición Química
La química, conforme a las normas ASTM A240 y ASME SA-240:
Los datos son típicos y no deberán interpretarse como los valores máximos o mínimos de especificación o de diseño final. Los datos de cualquiera pieza de material pueden variar de los datos mostrados aquí.
Resistencia a la Corrosión
Corrosión General
Las Aleaciones 304, 304L, y 304H austeníticas
de acero inoxidable proporcionan una resistencia
útil a la corrosión en una gama
amplia de ambientes moderadamente oxidantes a
moderadamente reductores. Las Aleaciones se usan
ampliamente en equipos y utensilios para procesar
alimentos, bebidas, y productos lácteos.
Los intercambiadores de calor, tuberías,
tanques y otros equipos de proceso que están
en contacto con el agua también utilizan
estas Aleaciones.
El 18 a 19 por ciento de Cromo que contienen estas Aleaciones proporciona resistencia a los ambientes oxidantes tales como el ácido nítrico diluido como se ilustra a continuación en los datos de la Aleación 304.
% Ácido Nítrico | Temperatura °F (°C) |
Tasa de Corrosión Mils/Yr (mm/a) |
10 | 300 (149) | 5.0 (0.13) |
20 | 300 (149) | 10.1 (0.25) |
30 | 300 (149) | 17.0 (0.43) |
Las Aleaciones 304, 304L, y 304H también son resistentes a los ácidos orgánicos moderadamente agresivos tales como el acético y ácidos reductores tales como el fosfórico. El 9 a 11 por ciento de Níquel contenido en estas Aleaciones de 18-8 ayuda a proporcionar una resistencia a los ambientes moderadamente reductores. Los ambientes más altamente reductores como el hervor de los ácidos clorhídrico y sulfámico diluidos son, según se ha visto, demasiado agresivos para estos materiales. Hervir en 50% cáustico también es demasiado agresivo.
En algunos casos, la Aleación 304L al bajo Carbono puede mostrar una Tasa de Corrosión menor que la Aleación 304 de más alto Carbono. Los datos para los ácidos fórmico, sulfámico , y el hidróxido de sodio son ilustraciones de esto. A lo contrario, se puede considerar que las Aleaciones 304, 304L, y 304H funcionan igualmente en la mayoría de los ambientes corrosivos. Una excepción notable son los ambientes suficientemente corrosivos como para causar corrosión intergranular en las soldaduras y las zonas afectadas por el calor en Aleaciones susceptibles. La Aleación 304L es preferible para usarse en estos medios, en los que hay condiciones de soldadura puesto que el bajo nivel de Carbono eleva la resistencia a la corrosión intergranular.
Corrosión Intergranular
La exposición de los aceros inoxidables
austeníticos 18-8 a Temperaturas en el
rango de 800°F a 1500°F (427°C a 816°C)
puede causar la precipitación de Carburos
de Cromo en las fronteras de los granos. Dichos
aceros están "sensibilizados"
y sujetos a la Corrosión Intergranular
al exponerse a ambientes agresivos. El contenido
de Carbono de la Aleación 304 puede permitir
que ocurra la sensibilización por las condiciones
térmicas experimentadas en la soldadura
autógena y las zonas de soldadura afectadas
por el calor. Por esta razón, la Aleación
304L de bajo Carbono es la preferida para aplicaciones
en las cuales el material se pone en servicio
en condiciones de "tal como se soldó".
El bajo contenido de Carbono extiende el tiempo
necesario para que se precipite un nivel pernicioso
de Cromo-carburos pero no elimina la reacción
de precipitación en materiales sometidos
por tiempos prolongados dentro de los rangos de
temperatura de precipitación.
Pruebas de Corrosión Intergranular | ||
ASTM
A262 Prueba de Evaluación |
Tasa de Corrosión, Mils/Yr (mm/a) | |
304 | 304L | |
Práctica
E Metal Base Soldado |
No Fisuras en
Doblez Algunas Fisuras en Soldadura (inaceptable) |
No Fisuras No Fisuras |
Práctica
A Metal Base Soldado |
Estructura Escalonada en Zanja (inaceptable) |
Estructura Escalonada Estructura Escalonada |
Agrietamiento por Corrosión al
Esfuerzo
Las Aleaciones 304, 304L, y 304H son las más
susceptibles de los aceros inoxidables austeníticos
al agrietamiento por corrosión al esfuerzo
o SCC (por las siglas en inglés de stress
corrosion cracking ) en los haluros debido a su
relativamente bajo contenido de Níquel.
Las condiciones que causan SCC son: (1) presencia
de iones de haluro (generalmente de cloruro),
(2) esfuerzos residuales a la tensión,
y (3) Temperaturas en exceso de los 120°F
(49°C). Los esfuerzos pueden ser resultados
de una deformación fría de la Aleación
durante el formado o por los rodillos expandiendo
tubos para hacer lámina de tubo, o por
las operaciones de soldadura que producen esfuerzos
por los ciclos térmicos usados. El nivel
de estos esfuerzos puede reducirse reviniendo
o liberando los esfuerzos del tratamiento térmico
después de la deformación en frío,
y así reducir la sensibilidad al SCC por
haluros. El bajo Carbono de la Aleación
304L es una elección mejor de material
para dar servicio en su condición liberada
de esfuerzos en ambientes que podrían causar
Corrosión Intergranular.
Haluro (Pruebas de Corrosión por Esfuerzo de Cloruro) | ||
Prueba | Muestras con Doblez en U (Muy Esforzadas) | |
304 | ||
33% Cloruro de Litio, Hirviendo |
Metal Base Soldado |
Agrietado, 14 a 96 Horas Agrietado, 18 a 90 Horas |
26% Cloruro de Sodio, Hirviendo |
Metal Base Soldado |
Agrietado, 142 a 1004 Horas Agrietado, 300 a 500 Horas |
40% Cloruro de Calcio, Hirviendo | Metal Base | Agrietado,
144 Horas -- |
Temperatura
Ambiente Exposición Marina (Costera) |
Metal
Base
Soldado |
Sin Agrietar |
Picaduras/Corrosión en Hendiduras
Las Aleaciones 18-8 han sido utilizadas con mucho
éxito en agua dulce con bajo contenido
del ion cloruro. Generalmente se considera que
100 ppm de cloruro es el límite de las
Aleaciones 18-8 particularmente si hay hendiduras
presentes. Para niveles mayores de cloruro, el
bajo pH y /o mayores Temperaturas, deben considerarse
las Aleaciones con mayor contenido de molibdeno
como la Aleación 316 . Las Aleaciones 18-8
no se recomiendan para ser expuestas a los ambientes
marinos.
Propiedades Físicas:
Densidad:
0.285 lb/in3 (7.90 g/cm3)
Módulo de Elasticidad a la Tensión:
29 x 106 psi (200 GPa)
Coeficiente Lineal de Expansión Térmica:
Rango de Temperatura | Coeficientes | ||
°F | °C | in/in/°F | cm/cm/°C |
68-212 | 20-100 | 9.2 x 10-6 | 16.6 x 10-6 |
18 - 1600 | 20 - 870 | 11.0 x 10-6 | 19.8 x 10-6 |
Conductividad Térmica:
Rango de Temperatura | Btu/hr/ft/°F | W/m/K | |
°F | °C | ||
212 | 100 | 9.4 | 16.3 |
932 | 500 | 12.4 | 21.4 |
El coeficiente general de transferencia de calor de los metales es determinado por factores además de la conductividad térmica del metal. La Capacidad de los grados de acero inoxidable de 18 -8 para mantener limpias las superficies con frecuencia permite una mejor transferencia de calor que otros metales con una mayor conductividad térmica.
Calor Específico:
°F | °C | Btu/lb/°F | J/kg/K |
32-212 | 0-100 | 0.12 | 500 |
Permeabilidad Magnética:
Las Aleaciones 18-8 son generalmente no magnética
en su condición revenida con valores de
permeabilidad magnética típicos
por debajo de 1.02 a 200H. Los valores de permeabilidad
varían con la composición y se incrementan
con el trabajo en frío.
Porcentaje de Trabajo Frío | Permeabilidad Magnética | |
304 | 304L | |
0 | 1.005 | 1.015 |
10 | 1.009 | 1.064 |
30 | 1.163 | 3.235 |
50 | 2.291 | 8.480 |
Propiedades Mecánicas
Propiedades Mecánicas a la Temperatura Ambiente
Las propiedades mecánicas mínimas
para las Aleaciones 304 y 304L revenidas de placa
de acero inoxidable austenítico, según
lo exigen las especificaciones de la ASTM A240
y la especificación ASME SA-240 se muestran
a continuación.
Propiedad | Propiedades
Mecánicas Mínimas Requeridas por ASTM A240 & ASME SA-240 |
||
304 | 304L | 304H | |
0.2%
Compensación en Rendimiento de Resistencia, psi MPa |
30,000 205 |
25,000 170 |
30,000 205 |
Resistencia
Última a la Tensión , psi MPa |
75,000 515 |
70,000 485 |
75,000 515 |
Porcentaje
de Elongación en 2 in. ó 51 mm |
40.0 |
40.0 |
40.0 |
Dureza, Máxima Brinell RB |
201 92 |
201 92 |
201 92 |
Propiedades a Bajas y Altas Temperaturas
Abajo se muestran los datos de las propiedades
típicas de resistencia a la tensión
para bajas y altas Temperaturas. A Temperaturas
de 1000°F (538°C) o superiores, hay que
considerar rupturas por esfuerzo y movimiento
longitudinal. Abajo se muestran los datos típicos
de rupturas por movimiento longitudinal y por
esfuerzo:
Temperatura de Prueba |
0.2% Resistencia |
Resistencia a la Tensión |
Elongación | |||
°F | °C | psi | (MPa) | psi | (MPa) | Porcentaje en 2" ó 51mm |
-423 | -253 | 100,000 | 690 | 250,000 | 1725 | 25 |
-320 | -196 | 70,000 | 485 | 230,000 | 1585 | 35 |
-100 | -79 | 50,000 | 354 | 150,000 | 1035 | 50 |
70 | 21 | 35,000 | 240 | 90,000 | 620 | 60 |
400 | 205 | 23,000 | 160 | 70,000 | 485 | 50 |
800 | 427 | 19,000 | 130 | 66,000 | 455 | 43 |
1200 | 650 | 15,500 | 105 | 48,000 | 330 | 34 |
1500 | 815 | 13,000 | 90 | 23,000 | 160 | 46 |
Resistencia al Impacto
Los aceros inoxidables austeníticos revenidos
mantienen una alta resistencia a los impactos
aún a temperaturas criogénicas,
propiedad que, en combinación con su resistencia
a bajas Temperaturas y fabricabilidad, ha conducido
a su uso en el manejo de gas natural licuado y
otros ambientes criogénicos. A continuación
se muestran los datos Típicos de Impacto
Charpy en Muesca V.
Temperatura | Energía Absorbida Charpy Muesca V | ||
°F | °C | Pies - libras | Joules |
75 | 23 | 150 | 200 |
-320 | -196 | 85 | 115 |
-425 | -254 | 85 | 115 |
Resistencia a la Fatiga
El límite de resistencia a la fatiga o
aguante es el esfuerzo máximo bajo del
cual el material probablemente no falle en 10
millones de ciclos en el ambiente al aire. La
resistencia a la fatiga en los aceros inoxidables
austeníticos, como grupo, es de típicamente
35% de la resistencia a la tensión. Se
experimentan variaciones sustanciales en los resultados
en servicio dado que hay variables adicionales
que influyen a la resistencia a la fatiga. Por
ejemplo, una lisura mayor en la superficie aumenta
la resistencia, en tanto que un ambiente más
corrosivo en servicio reduce la resistencia.
Soldadura
Los aceros inoxidables austeníticos consideran como los más soldables de los aceros de alta-aleación y se pueden soldar por todos los procesos de soldadura de fusión y resistencia. Las Aleaciones 304 y 304L son típicas de los aceros inoxidables austeníticos.
Dos cosas importantes a considerar al estar produciendo juntas soldadas con los aceros inoxidables austeníticos son: 1) preservar la resistencia a la corrosión, y 2) evitar las grietas.
Se produce un Gradiente de Temperatura en el material que se está soldando, que varía desde arriba de la temperatura de fusión en la charca de material fundido hasta la temperatura ambiente a cierta distancia de la soldadura. Entre más elevado sea el nivel de Carbono del material que se esté soldado, mayor será la probabilidad de que el ciclo térmico de la soldadura produzca como resultado la precipitación de Carburo de Cromo lo cual es nocivo para la resistencia a la corrosión. Para proporcionar un material al nivel mejor de resistencia a la corrosión, deben usarse materiales de bajo Carbono (Aleación 304L) cuando el material se vaya a poner en servicio en la condición de soldado. Alternativamente, un recocido completo disuelve el carburo de cromo y restaura un material de alto nivel de resistencia a la corrosión al de los materiales de contenido estándar de Carbono.
El metal de soldadura con una estructura completamente austenítica es más susceptible al agrietamiento durante la operación de soldado. Por esta razón, las Aleaciones 304 y 304L están diseñadas para solidificarse de nuevo con una cantidad pequeña de ferrita para minimizar la susceptibilidad a la formación de grietas.
La Aleación 309 (23% Cr - 13.5% Ni) o los metales de relleno basados en Níquel se utilizan para unirse a las Aleaciones austeníticas 18-8 al Acero al Carbono.
Tratamiento Térmico
Los aceros inoxidables austeníticos se tratan térmicamente para eliminar los efectos del rolado en frío o para disolver los carburos de cromo precipitados. El tratamiento térmico más seguro para lograr ambos requerimientos es el recocido en solución que se efectúa a temperaturas de 1850°F a 2050°F (1010°C a 1121°C). El enfriado de la temperatura de recocido debe ser a velocidades suficientemente altas en el rango de 1500-800°F (816°C - 427°C) para evitar la re-precipitación de los Cromocarburos.
Estos materiales no se pueden endurecer mediante tratamiento térmico.
Tratamiento Térmico
LimpiezaA pesar de su resistencia a la corrosión los aceros inoxidables necesitan cuidarse durante la fabricación y el uso para mantener su apariencia superficial aún bajo condiciones de servicio normales .
Al soldar, se usan gases de proceso inertes. La escoria o cascarilla que se forma por el proceso de soldado se quita con un cepillo de alambre de acero inoxidable. Los cepillos normales de alambre de acero al carbono dejan partículas de acero al carbono en la superficie y estas con el tiempo producirán herrumbre superficial. Para aplicaciones más severas, las áreas soldadas deberán tratarse con una solución desincrustante como una mezcla de ácidos nítrico y fluorhídrico los cuales habrá que lavar posteriormente.
Para materiales expuestos tierra adentro, o en servicio industrial ligero o medio, el mantenimiento requerido es mínimo. Sólo las áreas cubiertas necesitan lavarse ocasionalmente con una corriente de agua a presión. En áreas industriales pesadas, es recomendable el lavado frecuente para remover los depósitos de tierra que pudieran con el tiempo causar corrosión y menoscabar la apariencia superficial del acero inoxidable.
Las manchas difíciles y los depósitos como la comida quemada, pueden retirarse tallando con un limpiador no abrasivo y un cepillo de fibra, una esponja o una fibra de acero inoxidable. La fibra de acero inoxidable dejará una marca permanente en las superficies lisas de acero inoxidable .
Muchos de estos usos del acero inoxidable implican limpiar o esterilizar con regularidad. El equipo se limpia con una sosa cáustica especialmente diseñada, un solvente orgánico, o soluciones ácidas tales como las de ácido fosfórico o sulfámico (los ácidos fuertemente reductores, tales como el fluorhídrico o el clorhídrico pueden ser dañinos para estos aceros inoxidables).
Las soluciones limpiadoras deben drenarse y las superficies de acero inoxidable deben enjuagarse vigorosamente con agua limpia.
El diseño puede auxiliar en la limpieza. Los equipos con esquinas redondas, filetes y carencia de hendiduras, son de limpieza más fácil al igual que las soldaduras bien rectificadas y pulidas.
NOTE: The information and data in this product data sheet are accurate to the best of our knowledge and belief, but are intended for informational purposes only, and may be revised at any time without notice. Applications suggested for the materials are described only to help readers make their own evaluations and decisions, and are neither guarantees nor to be construed as express or implied warranties of suitability for these or other applications.