Placa de Acero Inoxidable
Sandmeyer Steel lleva existencias de la Aleación 310/310S de placa de acero inoxidable resistente al calor en espesores desde 3/16" hasta 3".
3/16" | 1/4" | 5/16" | 3/8" | 1/2" | 5/8" | 3/4" | 1" |
---|---|---|---|---|---|---|---|
4.8mm | 6.3mm | 7.9mm | 9.5mm | 12.7mm | 15.9mm | 19mm | 25.4mm |
1 1/4" | 1 1/2" | 1 3/4" | 2" | 2 1/4" | 2 1/2" | 3" | |
31.8mm | 38.1mm | 44.5mm | 50.8mm | 57.2mm | 63.5mm | 76.2mm |
La Aleación 310/310S (UNS S31000/S31008) de acero inoxidable austenítico típicamente se usa para aplicaciones de temperatura elevada. Su alto contenido de cromo y níquel proporciona una resistencia a la corrosión comparable, una resistencia superior a la oxidación y la retención de una mayor fracción de resistencia a la temperatura ambiente que la Aleación austenítica 304 común.
Especificaciones:
310/310S (UNS S31000) / (UNS S31008)
- Propiedades Generales
- Aplicaciones
- Composición Química
- PropiedadesFísicas
- Propiedades Mecánicas de Corto Plazo Típicas
- Resistencia a la Corrosión Acuosa
- Resistencia a la Oxidación a Temperaturas Elevadas
- Otras Formas de Degradación
- Características para la Fabricación
- Soldadura
- Tratamiento Térmico / Recocido
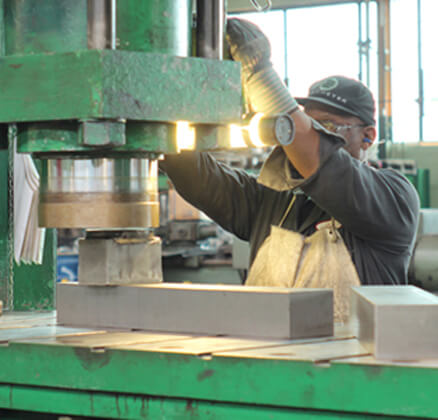
Propiedades Generales
La Aleación 309/309S y la Aleación 310/310S de acero inoxidable austenítico típicamente se usan para aplicaciones de temperatura elevada. Su alto contenido de cromo y níquel proporciona una resistencia a la corrosión comparable, una resistencia superior a la oxidación y la retención de una mayor fracción de resistencia a la temperatura ambiente que la Aleación austenítica 304 común.
Aplicaciones
Los aceros inoxidables de aleaciones mayores generalmente exhiben unaresistencia excelente a las temperaturas elevadas junto con una resistencia a la deformación por movimiento longitudinal y el ataque del medio ambiente. Como tales, se les usa ampliamente en la industria del tratamiento térmico para partes de hornos, tales como bandas transportadoras, rodillos, partes de quemadores, suporte para refractarios, retortas y forros de horno, abanicos, colgadores de tubos y cestos y bandejas para sostener piezas pequeñas. Estos grados además se usan en la industria de los procesos químicos para contener ácidos concentrados calientes, amoníaco y dióxido de sulfuro. En la industria de los alimentos procesados, se usan en contacto con ácidos acético y cítrico calientes.
Composición Química
Las características químicas corresponden a las especificaciones ASTM A<67 y ASTM A240 salvo indicación de lo contrario.
Aleación 309 | Aleación 309S | |
---|---|---|
(UNS S30900) | (UNS S30908) | |
C | 0.20 | 0.08 |
Mn | 2.00 | 2.00 |
P | 0.045 | 0.045 |
S | 0.030 | 0.030 |
Si | 0.75 | 0.75 |
Cr | 22.00 min/24.00 max | 22.00 min/24.00 max |
Ni | 12.00 min/15.00 max | 12.00 min/15.00 max |
Fe | Balance | Balance |
Aleación 310 | Aleación 310S | |
---|---|---|
(UNS S31000) | (UNS S31008) | |
C | 0.25 | 0.08 |
Mn | 2.00 | 2.00 |
P | 0.045 | 0.045 |
S | 0.030 | 0.030 |
Si | 1.75 | 1.50 |
Cr | 24.00 min/26.00 max | 24.00 min/26.00 max |
Ni | 19.00 min/22.00 max | 19.00 min/22.00 max |
Fe | Balance | Balance |
Composición de la Aleación- a valores en porciento de peso, niveles máximos salvo que se especifique un rango.
Propiedades Físicas
Aleación 309 | ||
---|---|---|
Densidad | lbm/in3 | g/cm3 |
at 68°F (20°C) | 0.29 |
8.03 |
Coeficiente de Expansión Térmica | (min/in)•°F | (mm/m)•°K |
at 68
- 212°F (20 - 100°C) |
8.7 | 15.6 |
at 68
- 932°F (20 - 500°C) |
9.8 | 17.6 |
at 68
- 1832°F (20 - 1000°C) |
10.8 | 19.4 |
Resistividad Eléctrica | mW•in | mW•cm |
at 68°F (20°C) | 30.7 | 78.0 |
at 1200°F (648°C) | 45.1 | 114.8 |
Conductividad Térmica | Btu/hr•ft•°F | W/m•K |
at 68
- 212°F (20 - 100°C) |
9.0 | 15.6 |
at 68
- 932°F (20 - 500°C) |
10.8 | 18.7 |
Calor Específico | Btu/lbm•°F | J/kg•K |
at 32
- 212°F (0 - 100°C) |
0.12 | 502 |
Permeabilidad Magnética (recocido)1 | ||
at 200H | 1.02 | |
Módulo de Elasticidad (recodico)2 | psi | GPa |
in tension (E) | 29 x 106 |
200 |
in shear (G) | 11.2 x 106 | 77 |
Aleación 310 | ||
---|---|---|
Densidad | lbm/in3 | g/cm3 |
at 68°F (20°C) | 0.29 |
8.03 |
Coeficiente de Expansión Térmica | (min/in)•°F | (mm/m)•°K |
at 68
- 212°F (20 - 100°C) |
8.8 | 15.9 |
at 68
- 932°F (20 - 500°C) |
9.5 | 17.1 |
at 68
- 1832°F (20 - 1000°C) |
10.5 | 18.9 |
Resistividad Eléctrica | mW•in | mW•cm |
at 68°F (20°C) | 30.7 | 78.0 |
at 1200°F (648°C) | -- | -- |
Conductividad Térmica | Btu/hr•ft•°F | W/m•K |
at 68
- 212°F (20 - 100°C) |
8.0 | 13.8 |
at 68
- 932°F (20 - 500°C) |
10.8 | 18.7 |
Calor Específico | Btu/lbm•°F | J/kg•K |
at 32
- 212°F (0 - 100°C) |
0.12 | 502 |
Permeabilidad Magnètica (recocido)1 | ||
at 200H | 1.02 | |
Módulo de Elasticidad (recocido)2 | psi | GPa |
in tension (E) | 29 x 106 |
200 |
in shear (G) | 11.2 x 106 | 77 |
1 Valor común
para ambas aleaciones, sin unidades
2 Valor común para ambas aleaciones
Propiedades físicas generales de la base de la Aleación 309 y la Aleación 310 de acero inoxidable austenítico.
Propiedades Mecánicas Típicas de Corto Plazo
Todas las pruebas de tensión se hicieron de conformidad con la ASTM E8. Los datos consisten en los resultados promedio de un mínimo de dos y hasta diez muestras. La resistencia a punto cedente fue determinada por el método de compensación de 0.2%. La elongación plástica se mide en una longitud de calibración de dos pulgadas.
Aleación 309
Temperatura de Prueba | Resistencia a Punto Cedente | Resistencia a la Tensión | Elongación | |||
---|---|---|---|---|---|---|
(°F) | (°C) | ksi | MPa | ksi | MPa | % |
77 | 25 | 42.0 | 290 | 90.0 | 621 | 49 |
400 | 204 | 35.0 | 241 | 80.0 | 552 | 46 |
800 | 427 | 30.0 | 207 | 72.0 | 497 | 40 |
1000 | 538 | 24.0 | 166 | 66.0 | 455 | 36 |
1200 | 649 | 22.0 | 152 | 55.0 | 379 | 35 |
1400 | 760 | 20.0 | 138 | 36.0 | 248 | 40 |
1600 | 871 | 18.5 | 128 | 21.0 | 145 | 50 |
1800 | 982 | -- | -- | 10.1 | 69 | 65 |
Aleación 309S
Temperatura de Prueba | Resistencia a Punto Cedente | Resistencia a la Tensión | Elongación | |||
---|---|---|---|---|---|---|
(°F) | (°C) | ksi | MPa | ksi | MPa | % |
77 | 25 | 50.9 | 351 | 97.1 | 670 | 44.6 |
200 | 93 | 44.7 | 308 | 88.8 | 612 | 29.0 |
400 | 204 | 37.4 | 258 | 81.7 | 563 | 34.5 |
600 | 316 | 33.4 | 230 | 80.2 | 553 | 31.6 |
800 | 427 | 29.6 | 204 | 77.1 | 531 | 32.1 |
900 | 482 | 30.4 | 210 | 74.7 | 515 | 32.0 |
1000 | 538 | 26.7 | 184 | 71.2 | 491 | 26.6 |
1100 | 593 | 26.5 | 182 | 65.6 | 452 | 25.5 |
1200 | 649 | 24.7 | 170 | 55.9 | 386 | 28.8 |
1300 | 704 | 23.7 | 163 | 55.7 | 384 | -- |
1400 | 760 | 22.2 | 153 | 36.0 | 248 | 22.5 |
1500 | 816 | 20.1 | 138 | 24.7 | 170 | 64.8 |
1600 | 871 | 16.6 | 114 | 20.7 | 142 | 73.3 |
1700 | 927 | 13.1 | 90 | 15.4 | 106 | 78.7 |
1800 | 982 | 8.2 | 56 | 10.8 | 74 | -- |
1900 | 1038 | 4.6 | 32 | 6.6 | 46 | -- |
Aleación 310
Temperatura de Prueba | Resistencia a Punto Cedente | Resistencia a la Tensión | Elongación | |||
---|---|---|---|---|---|---|
(°F) | (°C) | ksi | MPa | ksi | MPa | % |
77 | 25 | 42.4 | 292 | 89.5 | 617 | 45 |
400 | 204 | 31.5 | 217 | 76.6 | 528 | 37.5 |
800 | 427 | 27.2 | 188 | 74.8 | 516 | 37 |
1000 | 538 | 24.2 | 167 | 70.1 | 483 | 36 |
1200 | 649 | 22.6 | 156 | 57.2 | 394 | 41.5 |
1500 | 816 | 19.7 | 136 | 30.3 | 209 | 66 |
1800 | 982 | -- | -- | 11.0 | 76 | 65 |
2000 | 1093 | -- | -- | 7.0 | 48 | 77 |
Aleación 310S
Temperatura de Prueba | Resistencia a Punto Cedente | Resistencia a la Tensión | Elongación | |||
---|---|---|---|---|---|---|
(°F) | (°C) | ksi | MPa | ksi | MPa | % |
77 | 25 | 45.6 | 314 | 90.5 | 624 | 42.6 |
200 | 93 | 41.4 | 286 | 83.4 | 575 | 41.3 |
400 | 204 | 36.9 | 254 | 77.3 | 533 | 35.8 |
600 | 316 | 34.6 | 239 | 75.2 | 519 | 35.0 |
800 | 427 | 30.3 | 209 | 73.6 | 508 | 33.5 |
1000 | 538 | 29.4 | 203 | 70.2 | 484 | 37.0 |
1200 | 649 | 25.8 | 178 | 57.0 | 393 | 32.0 |
1400 | 760 | 21.4 | 147 | 37.7 | 260 | 54.0 |
1600 | 871 | 16.1 | 111 | 22.5 | 155 | 56.5 |
1800 | 982 | 8.2 | 56 | 11.8 | 81 | 93.3 |
2000 | 1093 | 4.0 | 27 | 6.5 | 44 | 121.0 |
Resistencia a la Corrosión Acuosa
Las Aleaciones309/309S y 310/310S se usan principalmente a temperatura elevada para aprovechar su resistencia a la oxidación. Sin embargo, ambos grados de acero inoxidable son resistentes a la corrosión acuosa debido a su alto contenido de cromo y níquel.
Aunque su mayor contenido de níquel ofrece una mejor marginal con respecto al agrietamiento por corrosión de esfuerzo por cloruro (SCC por las siglas en inglés de chloride stress corrosion cracking) en comparación con las aleaciones de aceros inoxidables de 18-8. Las Aleaciones 309/309S y 310310S de acero inoxidable austenítico siguen siendo susceptibles a esta forma de ataque.
Ciertas aplicaciones especifican el uso de aleaciones de acero inoxidable 310/310S cuando se necesita una resistencia mayor a la corrosión acuosa. Un ejemplo es el servicio en ácido nítrico concentrado, donde puede ocurrir un ataque preferencial de las fronteras de los granos.
Resistencia a la Oxidación a Temperaturas Elevadas
Las aleaciones metálicas reaccionan con su entorno hasta cierto grado bajo la mayoría de las condiciones. La reacción más común es la oxidación - los elementos metálicos se combinan con el oxígeno para formar óxidos. Los aceros inoxidables son resistentes a la oxidación a través de una oxidación selectiva del cromo que forma un óxido de crecimiento lento muy estable o Cr2O3 o cromia. Habiendo suficiente cromo en la aleación subyacente, se establece una capa superficial de óxido de cromo compacta y adherente, que previene la formación de otros óxidos de crecimiento más rápido y sirve como barrera a la degradación mayor. La velocidad de oxidación es controlada por el transporte de especies cargadas por la laminilla o cascarilla externa de cromia. Conforme se engruesa la cascarilla superficial la velocidad de oxidación disminuye dramáticamente porque las especies cargadas tienen que viajar más lejos. Este proceso, análogo de alta temperatura de la pasivación durante la corrosión a bajas temperaturas, se conoce como formación de cascarilla protectora.
La resistencia a la oxidación de los aceros inoxidables austeníticos se puede aproximar por el contenido de cromo de la aleación. Las aleaciones verdaderamente resistentes al calor generalmente contienen por lo menos un 20% (por peso) de cromo. Reemplazar el hierro con níquel también generalmente mejorá el comportamiento a la alta temperatura de una aleación. Las Aleaciones 309/309S y 310/310S son materiales sumamente aleados y por lo tanto muy resistentes a la oxidación.
Una muestra de metal oxidado incrementa su peso en correspondencia a la cantidad de oxígeno incorporado a la cascarilla y la oxidación interna que hubiere. Medir el cambio en el peso de una muestra que ha sido expuesta a altas temperaturas por un período de tiempo fijo es uno de los modos de determinar la resistencia a la oxidación de una aleación. Un mayor aumento de peso típicamente indica una oxidación más severa.
La oxidación es más compleja que el engrosamiento sencillo de la cascarilla. El descostrado o desprendimiento de la cascarilla de óxido superficial, es el problema que más comúnmente se encuentra durante la oxidación de los aceros inoxidables. El descostrado típicamente se manifiesta por una pérdida de peso rápidamente acelerada. Una diversidad de factores puede causar el descostrado, entre los más importantes figuran el ciclado térmico, los daños mecánicos y el espesor excesivo del óxido.
Durante la oxidación, el cromo se liga en la cascarilla en la forma de óxido de cromo. Cuando se descostra la cascarilla de óxido, se expone el metal fresco y la velocidad local de oxidación se incrementa temporalmente conforme se forma nuevo óxido de cromo. Si hay suficiente descostrado de la cascarilla, puede perderse suficiente cromo para causar que la aleación subyacente pierda sus propiedades de resistencia térmica. El resultado es la formación de óxidos de crecimiento rápido de hierro y níquel conocidos como oxidación galopante.
La oxidación a muy altas temperaturas puede conducir a la volatilización de la cascarilla. La cascarilla superficial de óxido de cromo formada en los aceros inoxidables resistentes al calor es principalmente Cr2O3. A temperaturas más altas, la tendencia es que se oxide más hasta convertirse en CrO3, que tiene una presión de vapor muy alta. La velocidad de oxidación entonces se divide en dos partes - el engrosamiento de la cascarilla por la formación del Cr2O3 y el efecto adelgazante de la evaporación del CrO3. La tendencia es que finalmente se llegue a un balance entre el crecimiento y el adelgazamiento permaneciendo la cascarilla a un espesor constante. Este resultado es la recesión continua de la superficie y consumo del metal inferior. El efecto de la volatilización de la cascarilla se convierte en un problema significativo a temperaturas superiores a unos 2000°F (1093°C) y se exacerba con los gases que fluyen rápidamente.
Otras Formas de Degradación
Otras especies fuera del oxígeno presente en el ambiente de alta temperatura pueden causar una degradación acelerada de los aceros inoxidables. La presencia de azufre puede conducir a un ataque de sulfidación. La sulfidación de los aceros inoxidables es un proceso complejo que depende fuertemente de los niveles relativos de azufre y oxígeno, junto con la forma del azufre presente (por ejemplo, vapor elemental, óxidos de azufre, sulfuro de hidrógeno). E cromo forma óxidos y sulfuros estables. En presencia de compuestos de tanto oxígeno como azufre, una capa externa estable de óxido de cromo se forma con frecuencia, la que puede actuar como una barrera del ingreso del azufre. Sin embargo, el ataque de la sulfidación todavía puede ocurrir en las regiones en las que la cascarilla se ha dañado o despendido y de acuerdo con ciertas circunstancias, el azufre puede transportarse a través de una costra de cromia y formar fases internas de sulfuro de cromo. La sulfidación es elevada en las aleaciones que contienen una cantidad significativa de níquel (25% o más). El níquel y sulfuro de níquel forman una fase eutéctica de bajo punto de fusión que puede causar un daño catastrófico a la aleación subyacente a temperaturas elevadas.
Los altos niveles de especies portadoras de carbono en el ambiente pueden producir como resultado el ingreso de carbono y la subsiguiente formación de carburos internos. La carburización generalmente ocurre a temperaturas por encima de los 1470|F (800°C) y a una actividad de carbón de menos de la unidad. La formación de una zona de metal internamente carburizado puede causar cambios no deseados en las propiedades mecánicas y físicas. Generalmente, la presencia de oxígeno previene el ingreso del carbón por la formación de una costra protectora externa. Los mayores niveles de níquel y silicio son tantos efectivos en reducir la susceptibilidad a la carburización. La pulverización metálica es una forma específica de ataque de carburización que generalmente ocurre a temperaturas más bajas (660-1650°F or 350-900°C) y a una actividad de carbón de mayor que la unidad. Puede producir como resultado un ataque local catastrófico por vía de la formación de profundos cráteres a través de un mecanismo complejo que convierte al metal macizo en una mezcla de grafito y partículas de metal.
La nitridación puede ocurrir en la presencia de gas nitrógeno. Los óxidos generalmente son más estables que los nitritos así que en una atmósfera que contiene oxígeno, típicamente se forma una cascarilla de óxido. Las capas de óxido son buenas barreras al ingreso de nitrógeno, así que la nitridación es rara vez una preocupación en el aire o en los gases típicos de los productos de combustión. La nitridación puede ser un problema en el nitrógeno purificado y es una preocupación especial en las atmósferas secas de amoniaco reformado donde el potencial de oxígeno es muy bajo. A temperaturas relativamente bajas generalmente se forma una película superficial de nitrito. A temperaturas altas (arriba de unos 1832°F o 1000°C) la difusividad del nitrógeno es suficientemente rápida para que el nitrógeno penetre profundamente en el metal y cause la formación de nitritos internos en las fronteras de los granos o dentro de los granos. Esto puede conducir a un compromiso de las propiedades mecánicas.
La inestabilidad metalúrgica o la formación de nuevas fases durante las exposiciones a las altas temperaturas puede afectar adversamente las propiedades mecánicas y reducir la resistencia a la corrosión. Las partículas de carburo tienden a precipitarse en las fronteras de los granos (sensibilización) cuando los aceros inoxidables austeníticos se mantienen en o se enfrían lentamente por un rango de temperaturas de 800-1650°F (427-899°C). Los mayores niveles de cromo y níquel contenidos en estas aleaciones producen como resultado una menor solubilidad del carbono, lo cual tiende a incrementar la susceptibilidad a la sensibilización. Se recomienda enfriar con un ahogador por inmersión (gas o líquido) por este rango crítico de temperaturas, particularmente para las secciones más gruesas. El tiempo a la temperatura requerido para formar carburos de cromo se incrementa conforme se reduce el contenido de carbono. Por lo tanto, las versiones de bajo carbono de estas aleaciones son más resistentes pero no inmunes a la sensibilización. Cuando se calientan a temperaturas de 1200-1850°F (649-1010°C) por períodos prolongados, las Aleaciones 309/309S y 320/320S pueden exhibir una ductilidad reducida a la temperatura ambiente debido a la precipitación de partículas quebradizas de la segunda fase (fase sigma y carburos). La fase sigma con frecuencia se forma en las fronteras de los granos y puede reducir la ductilidad. Este efecto es reversible y la ductilidad completa se puede restaurar volviendo a recocer a las temperaturas sugeridas.
La degradación por temperaturas elevadas es afectada en gran medida por la atmósfera presente y otras condiciones de operación. Los datos generales de oxidación sólo se pueden usar para estimar la resistencia relativa a la oxidación de las aleaciones diferentes. La Compañía Sandmeyer Steel puede proporcionar datos y experiencias previas correspondientes a aplicaciones específicas a solicitud.
Características para la Fabricación
Las Aleaciones 309/309S y 310/310S de acero inoxidable se utilizan ampliamente en las industrias de tratamiento / procesos térmicos debido a sus propiedades de alta temperatura y resistencia a la corrosión. Como tales, se les fabrica comúnmente para transformarlas en estructuras complejas. El acero dulce al carbono generalmente se le trata como el estándar para desempeño en la mayoría de las operaciones de forja metálica. Con respecto al acero al carbón, los aceros inoxidables austeníticos exhiben una diferencia significativa - son más aguantadores y tienden a endurecerse rápidamente al trabajarse. En tanto que esto no altera los métodos generales utilizados para cortar, maquinar, forjar, etc., si afecta las especificaciones de dichos métodos.
El corte y maquinado de los aceros inoxidables austeníticos se logra con facilidad utilizando las técnicas estándares típicamente empleadas para el acero dulce común con algunas modificaciones. Su comportamiento en el cortado puede ser bastante diferente - son más aguantadores y tienden a endurecerse rápidamente al trabajarse. Las virutas son como cordeles y resistentes y tienden a retener una ductilidad considerable. El herramental debe mantenerse afilado y sujetarse rígidamente. Generalmente se usan cortes más profundos y velocidades más lentas para cortar debajo de las zonas endurecidas por el trabajo. Debido a su baja conductividad térmica y alto coeficiente de expansión térmica inherente a los aceros inoxidables austeníticos, la remoción del calor y las tolerancias dimensionales tienen que tomarse en cuenta durante las operaciones de corte y maquinado.
Los aceros inoxidables austeníticos se forman fácilmente en frío mediante los métodos estándares tales como doblado, estirado, rolado, martillado, abocardado / achaflanado, girado, pantógrafo e hidroformado. Se endurecen fácilmente en el trabajo, lo cual se manifiesta por el incremento uniforme en la fuerza necesaria para continuar la deformación. Esto produce como resultado la necesidad de utilizar máquinas formadoras más fuertes y puede llegar a limitar la deformación posible sin crear grietas.
Un rango relativamente estrecho de temperaturas se puede usar para trabajar en caliente con eficacia las Aleaciones 309 y 310 debido a numerosos factores ambientales y metalúrgicos. La forja debe comenzar en el rango de temperaturas de 1800-2145°F (980-1120°C) y terminar antes de que se enfríe a 1800°F (980°C). Trabajar a temperaturas más elevadas produce como resultado una reducción de la ductilidad debido a factores ambientales y metalúrgicos, particularmente la formación de ferrita. Trabajar a temperaturas más bajas puede causar la formación de segundas fases quebradizas, como por ejemplo sigma y/o sensiblización. Después del forjado, la pieza trabajada debe enfriarse rápidamente a un calor negro.
Soldadura
Los aceros inoxidables de grado austenítico son los más soldables de los aceros inoxidables. Se les puede soldar utilizando todos los procesos comunes. Esto es generalmente cierto de las Aleaciones 309/309S y 310/310S. Cuando se requiere metal de relleno, generalmente se utilizan composiciones que concordantes. El contenido elevado de aleaciones de este grado puede hacer que la charca de soldadura se vuelva perezosa. Si la fluidez de la charca de soldadura es un problema un metal de relleno que contenga silicio puede ayudar (por ejemplo, ER309Si, ER309LSi).
Las Aleaciones 309/309S y 310/310S exhiben un coeficiente relativamente alto de expansión térmica y baja conductividad térmica y forman niveles bajos de ferrita en el metal al solidificar la soldadura. Estos factores pueden conducir a un agrietamiento caliente. El problema puede ser más severo en las juntas restringidas y/o anchas. El metal de relleno con un contenido más bajo de aleación (por ejemplo, ER308) incrementará la cantidad de ferrita en el depósito de soldadura y reducirá la tendencia al agrietamiento en caliente. La dilución subsiguiente del metal base puede reducir la resistencia a la corrosión / calor de la soldadura.
Los grados "S" son relativamente bajos en carbono. Con una práctica correcta de soldado, se hace poco probable la corrosión intergranular de la zona afectada por el calor. El tinte por calor o cascarilla debe removerse para asegurar la restauración completa de la resistencia a la corrosión cerca de la soldadura. El rectificar o cepillar con un cepillo de alambre de acero inoxidable puede usarse para eliminar la cascarilla de tinte por calor. El decapado con ácido también remueve el tinte por calor. Las piezas pequeñas pueden tratarse en un baño y las piezas mayores se pueden decapar localmente usando una pasta especial consistente en una mezcla de ácido nítrico y HF ó ácido clorhídrico suspendido en una carga inerte. Un lavado con agua completo debe seguir inmediatamente, cuidando de remover completamente todas las trazas de la pasta decapante.
Tratamiento Térmico / Recocido
La razón principal para recocer estas aleaciones es para producir una microestructura recristalizada con un tamaño de grano uniforme y para disolver los perniciosos precipitados de carburo de cromo. Para asegurar un recocido completo, las piezas deben mantenerse en el rango de 2050-2150°F (1120-1175°C) por aproximadamente 30 minutos (tiempo a la temperatura) por pulgada de espesor de la sección. Esta es una recomendación general únicamente - los casos específicos pueden requerir algo más de investigación. Cuando se recocen correctamente estos grados son primariamente austeníticos a la temperatura ambiente. Algunas cantidades pequeñas de ferrita pueden estar presentes.
La formación de cascarilla de óxido es inevitable durante el recocido al aire de las Aleaciones 309/309S y 310/310S. La cascarilla que se forma es generalmente rica en cromo y relativamente adherente. La cascarilla del recocido generalmente debe retirarse previo a un mayor procesado o puesta en servicio. Típicamente, existen dos métodos para retirar la cascarilla - el mecánico y el químico. Una combinación de esmerilado por chorro de la superficie antes de eliminar la cascarilla químicamente es generalmente efectiva para quitar toda menos la cascarilla más fuertemente adherida. La arena sílica o las cuentas de vidrio son buenas opciones de medios para la limpieza con chorro de arena. También se pueden usar rebabas de acero o hierro pero esto conduce a hierro libre empotrado en la superficie que puede posteriormente producir como resultado el herrumbre superficial o la decoloración a menos de que la superficie sea decapada subsiguientemente.
La remoción química de la cascarilla se realiza generalmente con una mezcla de ácidos nítrico y fluorhídrico. La composición del baño correcta y la temperatura correcta del proceso dependen de cada situación. Un baño de decapado típico que se usa consiste en 5-15% de HNO3 (65% de potencia inicial) y 1/2 - 3% de HF (60% de potencia inicial) en una solución acuosa. Mayores concentraciones de ácido fluorhídrico conducen a una remoción más agresiva de la cascarilla. Las temperaturas del baño generalmente varían de la temperatura ambienta hasta unos 140°F (50*C). Las temperaturas mayores producen como resultado un descascardo más rápido pero pueden atacar a las fronteras de los granos agresivamente, produciendo como resultado una superficie acanalada. Un lavado con agua completo debe seguir inmediatamente al decapado, cuidando de remover completamente todas las trazas de los ácidos decapantes. Luego el secado debe usarse para evitar manchas y tinciones.
Como se hizo notar, las Aleaciones 309/309S y 310/310S consisten únicamente de austenita a la temperatura ambiente - no se pueden endurecer mediante tratamiento térmico. Las resistencias mecánicas mayores se pueden lograr mediante el trabajo en frío o en caliente, pero estos grados generalmente no están disponibles en tales condiciones. Las mayores resistencias a la tensión y al punto cedente que se pueden obtener mediante el trabajo en frío no seguido después por un recocido completo no son estables a las mayores temperaturas a las cuales se utilizan frecuentemente estas aleaciones. Las propiedades de deslizamiento lateral en lo particular pueden ser afectadas adversamente por el uso de materiales trabajados en frío en temperaturas elevadas.
NOTE: The information and data in this product data sheet are accurate to the best of our knowledge and belief, but are intended for informational purposes only, and may be revised at any time without notice. Applications suggested for the materials are described only to help readers make their own evaluations and decisions, and are neither guarantees nor to be construed as express or implied warranties of suitability for these or other applications.