Placa de Acero Inoxidable
La Compañía Sandmeyer Steel tiene el mayor y más pesado inventario de placa de acero inoxidable en la Aleación 317, en espesores desde 3/16" hasta 3".
3/16" | 1/4" | 5/16" | 3/8" | 1/2" | 5/8" | 3/4" | 7/8" | 1" | 1 1/8" |
---|---|---|---|---|---|---|---|---|---|
4.8mm | 6.3mm | 7.9mm | 9.5mm | 12.7mm | 15.9mm | 19mm | 22.2mm | 25.4mm | 28.6mm |
1 1/4" | 1 1/2" | 1 3/4" | 2" | 2 1/4" | 2 1/2" | 2 3/4" | 3" | 3 1/2" | 4" |
31.8mm | 38.1mm | 44.5mm | 50.8mm | 57.2mm | 63.5mm | 69.9mm | 76.2mm | 88.9mm | 101.6mm |
La Aleación 317L (UNS S31703) es un acero inoxidable austenítico que lleva molibdeno con una resistencia mucho mayor a los ataques químicos en comparación con los aceros inoxidables austeníticos convencionales de níquel-cromo tales como la Aleación 304. Además, la Aleación 317L ofrece una mayor resistencia al alargamiento lateral, tensión a la ruptura, y a la tensión a temperaturas elevadas que los aceros inoxidables convencionales. Es un acero al bajo carbono o grado "L" que proporciona resistencia a la sensibilización durante el soldado y otros procesos térmicos.
Especificaciones:
317L (UNS S31703)
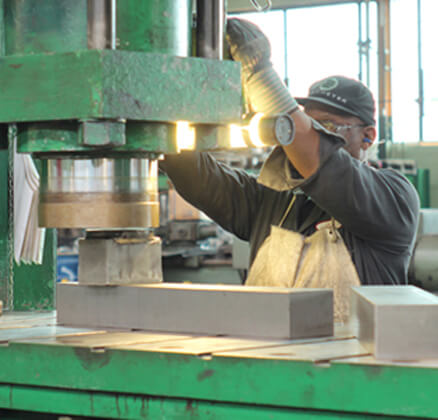
Propiedades Generales
La Aleación 317LMN y 317L es un acero inoxidable austenítico que lleva molibdeno con una resistencia mucho mayor a los ataques químicos en comparación con los aceros inoxidables austeníticos convencionales de níquel-cromo tales como la Aleación 304. Además, las Aleaciones 317LMN y 317L ofrecen una mayor resistencia al alargamiento lateral, tensión a la ruptura, y a la tensión a temperaturas elevadas que los aceros inoxidables convencionales. Todos son aceros al bajo carbono o grado "L" para ofrecer resistencia a la sensibilización durante el soldado y otros procesos térmicos. Las designaciones "M" y "N" indican que las composiciones contienen niveles incrementados de molibdeno y nitrógeno respectivamente. La combinación de molibdeno y nitrógeno es particularmente efectiva para mejorar la resistencia a las picaduras y la corrosión de las hendiduras, especialmente en corrientes de proceso que contienen ácidos, cloruros, y compuestos de azufre a temperaturas elevadas. El nitrógeno también sirve para incrementar la resistencia de estas aleaciones. Ambas aleaciones son para usarse en condiciones severas de servicio tales como para los sistemas de desulfurización de humos (FGD por las siglas en inglés de Flue Gas Desulfurization).
Composición
Composición Química en Porcentaje de Peso por ASTM A240 para las Aleaciones Citadas | ||
---|---|---|
Elemento | Tipo 317L | Tipo 317LMN |
Carbono | 0.03 max | 0.03 max |
Manganeso | 2.00 | 2.00 |
Silicio | 0.75 max | 0.75 max |
Cromo | 18.00 - 20.00 | 17.00 - 20.00 |
Níquel | 11.00 - 15.00 | 13.50 - 17.50 |
Molibdeno | 3.00 - 4.00 | 4.00 - 5.00 |
Fósforo | 0.04 max | 0.04 max |
Azufre | 0.03 max | 0.03 max |
Nitrógeno | 0.10 max | 0.10 - 0.20 |
Fierro | Balance | Balance |
UNS No. | S31703 | S31726 |
Resistencia a la Corrosión
Las Aleaciones 317L y 317LMN de acero inoxidable son más resistentes a la corrosión atmosférica y leve de otros tipos que los aceros convencionales de cromo-níquel. En general, los ambientes que no son corrosivos para los aceros 18Cr-8Ni no atacarán a las aleaciones que contienen molibdeno, a excepción de los ácidos sumamente oxidantes como el ácido nítrico.
Las Aleaciones 317LMN y 317L de acero inoxidable son bastante más resistentes a las soluciones de ácido sulfúrico que otros tipos de aceros convencionales de cromo-níquel. La resistencia se incrementa con el contenido de molibdeno. Estas aleaciones son resistentes a las concentraciones de ácido sulfúrico hasta 5 por ciento a temperaturas hasta 120°F (49°C). A temperaturas inferiores a los 100°F (38°C) estas aleaciones tienen excelente resistencia a soluciones de mayores concentraciones. No obstante, se recomienda hacer pruebas de servicio para considerar los efectos de las condiciones específicas de operación que pudieran afectar el comportamiento corrosivo. En los procesos en que ocurre la condensación de gases portadores de azufre, estas aleaciones son mucho más resistentes al ataque en el punto de condensación que la Aleación 316 convencional. La concentración de ácido tiene una influencia marcada en la velocidad de ataque a dichos ambientes y debe determinarse cuidadosamente mediante pruebas de servicio.
Las Aleaciones 317LMN y 317L de acero inoxidable son bastante más resistentes a las soluciones de ácido sulfúrico que otros tipos de aceros convencionales de cromo-níquel. La resistencia se incrementa con el contenido de molibdeno. Estas aleaciones son resistentes a las concentraciones de ácido sulfúrico hasta 5 por ciento a temperaturas hasta 120°F (49°C). A temperaturas inferiores a los 100°F (38°C) estas aleaciones tienen excelente resistencia a soluciones de mayores concentraciones. No obstante, se recomienda hacer pruebas de servicio para considerar los efectos de las condiciones específicas de operación que pudieran afectar el comportamiento corrosivo. En los procesos en que ocurre la condensación de gases portadores de azufre, estas aleaciones son mucho más resistentes al ataque en el punto de condensación que la Aleación 316 convencional. La concentración de ácido tiene una influencia marcada en la velocidad de ataque a dichos ambientes y debe determinarse cuidadosamente mediante pruebas de servicio.
Pruebas de Resistencia a la Corrosión en Soluciones Hirvientes y Pruebas de la ASTM | ||||
---|---|---|---|---|
Solución
de Prueba |
Tasa de
Corrosión en Mils por Año (mm/y)
para las Aleaciones Citadas |
|||
Aleación 316L |
Aleación 317L |
Aleación 317LMN |
Aleación 276 |
|
20% Ácido Acético |
0.12 (<0.01) |
0.48 (0.01) |
0.12 (<0.01) |
0.48 (0.01) |
45% Ácido Fórmico |
23.41 (0.60) |
18.37 (0.47) |
11.76 (0.30) |
2.76 (0.07) |
10% Ácido Oxálico |
48.03 (1.23) |
44.90 (1.14) |
35.76 (0.91) |
11.24 (0.28) |
20% Ácido Fosfórico |
0.06 (0.02) |
0.72 (0.02) |
0.24 (<0.01) |
0.36 (0.01) |
10% Ácido Sulfúrico |
635.7 (16.15) |
298.28 (7.58) |
157.80 (4.01) |
13.93 (0.35) |
10% Bisulfato de Sodio |
71.57 (1.82) |
55.76 (1.42) |
15.60 (0.40) |
2.64 (0.07) |
50% Hidróxido de Sodio |
77.69 (1.92) |
32.78 (0.83) |
85.68 (2.18) |
17.77 (0.45) |
ASTM
A262 Práctica B (FeSO4H2SO4) |
26.04 (0.66) |
20.76 (0.53) |
17.28 (0.44) |
264.5 (6.72) |
ASTM
A262 Práctica C (65% HNO3) |
22.31 (0.56) |
19.68 (0.50) |
16.32 (0.42) |
908.0 (23.06) |
ASTM
A262 Práctica E (Cu•CUSO4•H2SO4) |
Pasa | Pasa | Pasa | Pasa |
El bajo carbono de estas aleaciones (menos de 0.03%) efectivamente previene la sensibilización a la corrosión intergranular durante los procesos térmicos tales como soldadura o forjado. El contenido mayor de cromo de los aceros inoxidables 317LMN y Aleación 317L también ofrece una resistencia superior al ataque intergranular. Debe notar que la exposición prolongada en el rango de los 800 a 1400°F (427-800°C) puede ser pernicioso para la resistencia a la corrosión intergranular y también puede hacer que se vuelva quebradizo debido a la precipitación de la fase sigma. El mayor contenido de nitrógeno de la aleación 317LMN retarda la precipitación de la fase sigma así como también de los carburos.
Equivalentes de Resistencia a las Picaduras | |
---|---|
Aleación | PRE |
Aleación
316 |
25 |
Aleación 317L | 30 |
Aleación 317LMN | 38 |
Aleación 625 | 52 |
Aleación C276 | 69 |
Los altos contenidos de molibdeno y nitrógeno pueden significativamente mejorar la resistencia a las picaduras como se ilustra en la tabla anterior de Equivalentes de Resistencia a las Picaduras (PRE por las siglas en inglés de Pitting Resistance Equivalents). La PRE se basa en los resultados de las pruebas de corrosión en las cuales se encontró que el nitrógeno era 30 veces más efectivo que el cromo y aproximadamente 9 veces más efectivo que el molibdeno en elevar la resistencia a las picaduras por cloruro.
La temperatura del inicio de la corrosión de hendiduras según se determinó en una prueba modificada AST G-48B es un medio útil para jerarquizar la relativa resistencia de las aleaciones inoxidables y base níquel. La tabla que se presenta a continuación de Temperaturas Críticas de Corrosión de Hendiduras (Critical Crevice Corrosion Temperatures) demuestra que la resistencia a la corrosión de las hendiduras en los aceros inoxidables austeníticos se incrementa con el contenido de molibdeno y nitrógeno de la aleación.
Corrosión de Hendiduras
en Ambiente Simulado de Sistema FGD |
|||
---|---|---|---|
Aleación | Pérdida
de Peso (g/cm2) para Pruebas* a las Temperaturas Citadas |
||
24°C (75°F) |
50°C (122°F) |
70°C (158°F) |
|
Aleación
317L |
0.0007 |
0.0377 |
0.0500 |
Aleación 317LMN | 0.0000 | 0.0129 | 0.0462 |
Aleación 625 | 0.0000 | 0.0000 | 0.0149 |
Aleación C276 | 0.0000 | 0.0001 | 0.0004 |
**72exposición de 72 horas
con base en el procedimiento ASTM G-48B utilizando
la siguiente solución: 7 vol.%H2SO4, 3
vol%HCI, 1 wt% CuCl2, 1 wt%FeCl3
Resistencia a la Oxidación
Los aceros de cromo-níquel-molibdeno tienen todos una resistencia excelente a la oxidación y una baja tasa de formación de costra en atmósferas ordinarias a temperaturas hasta de 1600-1650°F (871-899°C).
Fabricación
Las propiedades físicas y mecánicas de los aceros inoxidables 317LMN y Aleación 317L son semejantes a las de aceros inoxidables austeníticos más convencionales y por lo tanto pueden fabricarse de manera semejante a las Aleaciones 304 y 316.
Tratamiento Térmico
Forja
El rango inicial de temperaturas recomendado es
de 2100-2200°F (1150-1205°C) con un rango
para acabar de 1700-1750°F (927-955°C).
Recocido
Los aceros inoxidables 317LMN y Aleación
317L pueden recocerse en el rango de temperaturas
de los 1975-2150°F (1080-1175°C) seguido
de un chorro de aire frío o baño
de agua, dependiendo del espesor. Las placas deben
recocerse entre los 2100°F (1150°C) y
2150°F (1175°C). El metal debe enfriarse
de la temperatura de recocido (desde el rojo/blanco
al negro) en menos de tres minutos.
Endurecibilidad
Estos grados no se pueden endurecer con tratamiento
térmico.
Soldadura
Se sugiere el uso de un filtro sobrealeado para mantener la resistencia a la corrosión en la condición de soldado como quedó. Se sugiere usar metales de relleno que contengan por lo menos 6% de molibdeno para soldar la Aleación 317L y un metal de relleno con por lo menos 8% de molibdeno, como la Aleación 625, para el 317LMN. En las aplicaciones en las que no es posible usar un metal de relleno sobrealeado o realizar un recocido posterior a la soldadura y tratamiento decapante, la severidad del ambiente de servicio debe considerarse detenidamente para determinar si las propiedades de las soldaduras autógenas (soldaduras hechas sin rellenos) son satisfactorias. La resistencia óptima a la corrosión de los aceros inoxidables 317LMN y aleación 317L soldados en forma autógena se obtiene mediante el recocido y decapado posterior a la soldadura. Se sugiere revisar la ASTM A-380 "Práctica Recomendada para Descostrar y Limpiar Superficies de Acero" para obtener mayor información.
Propiedades Mecánicas
En la tabla siguiente se muestran las propiedades mínimas a la tensión y dureza máxima para las placas recocidas, lámina y productos en tiras conforme a las especificaciones de la ASTM.
Propiedades
Mecánicas Mínimas según
La ASTM A-240 para las Aleaciones Citadas |
||
---|---|---|
Propiedad | Aleación 317L | Aleación 317LMN |
Resistencia
Última a la Tensión, ksi (MPa) |
75 (515) |
80 (550) |
0.2% Resistencia al Punto Cedente, ksi (MPa) | 30 (205) |
35 (240) |
% Elongación in 2" (5.1 cm) | 40 | 40 |
Dureza, Máximo | 217BHN | -- |
UNS No. | S31703 | S31726 |
Propiedades Físicas
Los datos de propiedades físicas que se dan a continuación representan a la clase de aceros inoxidables de hierro-cromo-níquel-molibdeno. Para todo efecto práctico, los datos son aplicables a los aceros inoxidables 317LMN y Aleación 317L. Todas las propiedades están a temperatura ambiente (68°F, 20°C) salvo indicación de lo contrario.
Densidad |
0.29 8.0 |
lb/in3 g/cm3 |
---|---|---|
Módulo de Elasticidad | 29•106 200 |
psi Gpa |
Rango de Fusión | 2410 to 2550 1320 to 1400 |
° F °C |
Conductividad
Térmica 68 to 212°F 20 to 100°C |
100.8 14.6 |
Btu/ft2-hr-°F-in Watts/m- K |
Coeficiente
Expansión Térmica 77°F (25°C) to: 212°F (100°C) 932°F (500°C) 1832°F (1000°C) |
9.2 (16.5) 10.1 (18.2) 10.8 (19.5) |
10-6/°F (10-6/°C) 10-6/°F (10-6/°C) 10-6/°F (10-6/°C) |
Calor Específico | 0.11 0.46 |
Btu/lb-°F J/g-°K |
Resistividad Eléctrica | 31.1 0.79 |
µ-ohm-in µ-ohm-in |
Permeabilidad
Magnética Fully annealed 0.5" plate 65% cold-worked 0.5" plate |
1.0028 1.0028 |
µ at H = 200 oe µ at H = 200 oe |
NOTE: The information and data in this product data sheet are accurate to the best of our knowledge and belief, but are intended for informational purposes only, and may be revised at any time without notice. Applications suggested for the materials are described only to help readers make their own evaluations and decisions, and are neither guarantees nor to be construed as express or implied warranties of suitability for these or other applications.