Placa de Acero Inoxidable
Sandmeyer Steel lleva existencias de la Aleación 321 de placa de acero inoxidable en espesores desde 3/16" hasta 3". También se puede ordenar una versión al alto carbono, la Aleación 321H (UNS 532109), en el mismo rango de espesores.
3/16" | 1/4" | 5/16" | 3/8" | 1/2" | 5/8" | 3/4" | 7/8" | 1" | 1 1/8" |
---|---|---|---|---|---|---|---|---|---|
4.8mm | 6.3mm | 7.9mm | 9.5mm | 12.7mm | 15.9mm | 19mm | 22.2mm | 25.4mm | 28.6mm |
1 1/4" | 1 1/2" | 1 3/4" | 2" | 2 1/4" | 2 1/2" | 2 3/4" | 3" | 3 1/2" | 4" |
31.8mm | 38.1mm | 44.5mm | 50.8mm | 57.2mm | 63.5mm | 69.9mm | 76.2mm | 88.9mm | 101.6mm |
La Aleación 321 (UNS S32100) es un acero inoxidable estabilizado que ofrece como su ventaja principal una resistencia excelente a la corrosión intergranular después de la exposición a temperaturas del rango de precipitación de carburo de cromo desde 800 hasta 1500°F (de 427 a 816°C). La Aleación 321 de acero inoxidable está estabilizada contra la formación de carburos de cromo por la adición de titanio.
La Aleación 321 de acero inoxidable también tiene ventanas por su servicio a altas temperaturas debido a sus buenas propiedades mecánicas. La Aleación 321 de acero inoxidable ofrece una mejor resistencia al desplazamiento longitudinal y las rupturas por tensión que la Aleación 304 y en particular la Aleación 304L, que también podrían considerarse para exposiciones donde se tiene preocupación por la sensibilización y la corrosión intergranular.
Especificaciones: 321/321H
(UNS S32100) / (UNS S532109)
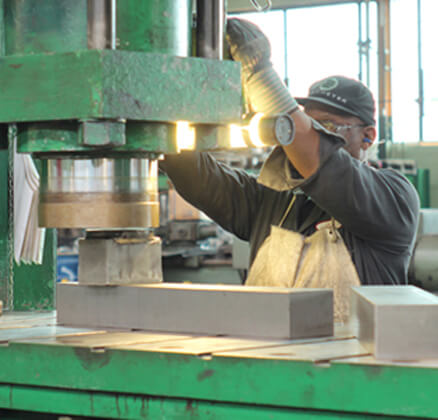
Propiedades Generales
Las Aleaciones 321 (UNS S32100) y 347 (S34700) son aceros inoxidables estabilizados que ofrecen como ventaja principal una resistencia excelente a la corrosión intergranular después de la exposición a temperaturas del rango de precipitación de carburo de cromo desde 800 hasta 1500°F (de 427 a 816°C). La Aleación 321 de acero inoxidable está estabilizada contra la formación de carburos de cromo por la adición de titanio. La Aleación 347 está estabilizada por la adición de columbio y tantálo.
En tanto que las Aleaciones 321 y 347 continúan empleándose para servicio prolongado en el rango de temperaturas de 800° a 1500° F (427° a 816° C), la Aleación 304L ha suplantado a estos grados estabilizados en aplicaciones que involucran sólo soldadura o calentamiento por un tiempo breve.
Las Aleaciones 321 y 347 de acero inoxidable también tienen ventajas por su servicio a altas temperaturas debido a sus buenas propiedades mecánicasLas Aleaciones 321 y 347 de acero inoxidable ofrecen mejores propiedades ante las deformaciones y rupturas por esfuerzos, que la Aleación 304L, que también podría ser considerada para exposiciones en las que preocupe la sensibilización y la corrosión intergranular. Esto da como resultado mayores esfuerzos permisibles a temperaturas elevadas en estas aleaciones estabilizadas para aplicaciones de Código ASME para Calderas y Recipientes Presurizados. Las Aleaciones 321 y 347 tienen temperaturas máximas de uso de 1500°F (816°C) para aplicaciones del código como la Aleación 304, en tanto que la Aleación 304L está limitada a 800°F (426°C).
Se tienen disponibles versiones de ambas aleaciones al alto carbono. Estos grados tienen designaciones UNS S32109 y S34709.
Composición Química
Representada por las Especificaciones ASTM A240 y ASME SA-240.
Elemento | Máximo Porcentaje de
Peso Salvo que se Especifique un Rango |
|
321 | 347 | |
Carbono* | 0.08 | 0.08 |
Manganeso | 2.00 | 2.00 |
Fósforo | 0.045 | 0.045 |
Azufre | 0.030 | 0.03 |
Sílice | 0.75 | 0.75 |
Cromo | 17.00-19.00 | 17.00-19.00 |
Níquel | 9.00-12.00 | 9.00-13.00 |
Columbo
+ Tántalo** |
-- | 10xC min to 1.00 max |
Tántalo | -- | -- |
Titanio** | 5x(C+N) min to 0.70 max | -- |
Cobalto | -- | -- |
Nitrógeno | 0.10 | -- |
Hierro | Balance | Balance |
También grado H con Carbono
0.04 - 0.10%. ** El grado H estabilizador mínimo es una fórmula diferente. |
Resistencia a la Corrosión
Corrosión General
Las Aleaciones 321 y 347 ofrecen una resistencia
a la corrosión general similar a la de
la aleación no estabilizada de Níquel
304. El calentamiento por períodos prolongados
en el rango de precipitación de carburo
de cromo puede afectar la resistencia general
de las Aleaciones 321 y 347 en medios severamente
corrosivos.
En la mayoría de los ambientes, ambas aleaciones mostrarán una resistencia a la corrosión similar. No obstante, la Aleación 321 en la condición recocida es un poco menos resistente a la corrosión general en ambientes fuertemente oxidantes que la Aleación 347 recocida. Por esta razón, la Aleación 347 es preferible para los ambientes acuosos y otros ambientes de baja temperatura.La exposición en el rango de temperaturas de 800°F a 1500°F (427°C a 816°C) reduce la resistencia general a la corrosión de la Aleación 321 en mayor medida que la Aleación 347. La Aleación 347 se usa primariamente en aplicaciones de alta temperatura en las que la alta resistencia a la sensibilización es esencial, y por lo tanto previene la corrosión intergranular a temperaturas bajas.
Corrosión Intergranular
Las Aleaciones 321 y 347 han sido desarrolladas
para aplicaciones enlas que los aceros no estabilizados
de cromo-níquel, tales como la Aleación
304 serían susceptibles a la corrosión
intergranular.
Cuando los aceros no estabilizados de cromo-níquel se mantienen o se enfrían lentamente en el rango de 800°F a 1500°F (427°C a 816°C), se precipita carburo de cromo en las fronteras del grano. En la presencia de ciertos medios fuertemente corrosivos, estas fronteras de grano son atacadas preferencialmente, produciendo un debilitamiento general del metal, y puede ocurrir una desintegración completa.
Los medios orgánicos o los agentes acuosos o condiciones atmosféricas débilmente corrosivos rara vez producen corrosión intergranular aún cuando estén presentes grandes cantidades de carburos precipitados. Cuando se solda el material de calibre delgado, el tiempo en el rango de temperaturas de 800°F a 1500°F (427°C a 816°C) es tan corto que con la mayoría de los medios corrosivos, los tipos no estabilizados son en general satisfactorios. La extensión a la cual la precipitación de carburos podría ser nociva, depende de la longitud de tiempo que la aleación haya estado expuesta al rango de 800°F a 1500°F (427°C a 816°C) y del ambiente corrosivo. Aún los tiempos de calentado más prologados involucrados en las operaciones de soldadura de calibres pesados, no son dañinos para las aleaciones de grado "L" no estabilizadas cuando el contenido de carbono se mantiene a niveles bajos de 0.03% o menos.
La alta resistencia de las Aleaciones 321 y 347 estabilizadas a la sensibilización y la corrosión intergranular es ilustrada por los datos para la Aleación 321 en la prueba de 16% Ácido Sulfúrico de cobre-cobre sulfato (ASTM A262, Práctica E)de más adelante. Las muestras recocidas en molino recibieron un tratamiento térmico sensibilizador consistente en remojo a 1050°F (566°C) por 48 horas antes de la prueba.
Prueba de Corrosión
Intergranular Resultados de Sensibilización* de Largo Plazo ASTM A262 Práctica E |
|||
Aleación | Tasa (imp) | Bend | Tasa de Doblez (mpy) |
304 | 0.81 | Disuelto | 9720.0 |
304L | 0.0013 | IGA | 15.6 |
*Recocido 1100°F, 240 horas
La ausencia de ataque intergranular (AIG) en muestras de la Aleación 347 demuestra que no se sensibilizaron durante esta exposición térmica. La baja tasa de corrosión exhibida por las muestras de Aleación 321 demuestra que aunque sufrió algo de AIG, fue más resistente que la Aleación 304L bajo estas condiciones. Todas estas aleaciones son muy superiores a la Aleación 304 regular de acero inoxidable bajo las condiciones de esta prueba.
En general, las Aleaciones 321 y 347 se usan para equipo soldado pesado que no se puede recocer y para equipo se opera entre 800°F y 1500°F (427°C y 816°C) o enfriado lentamente al pasar por este rango de temperatura.La experiencia adquirida en una amplia gama de condiciones de servicio nos ha proporcionado suficientes datos para predecir generalmente la posibilidad de ataque intergranular en la mayoría de las aplicaciones.
Favor de revisar también nuestros comentarios bajo la sección de Tratamiento Térmico.
Agrietamiento de Corrosión por Tensión
The Alloys 321 and 347 austenitic stainless steels
are susceptible to stress corrosion cracking (SCC)
in halides similar to Alloy 304 stainless steel.
This results because of their similarity in nickel
content. Conditions which cause SCC are: (1) presence
of halide ion (generally chloride), (2) residual
tensile stresses, and (3) environmental temperatures
in excess of about 120°F (49°C). Stresses
may result from cold deformation during forming
operations or from thermal cycles encountered
during welding operations. Stress levels may be
reduced by annealing or stress-relieving heat
treatments following cold deformation. The stabilized
Alloys 321 and 347 are good choices for service
in the stress relieved condition in environments
which might otherwise cause intergranular corrosion
for unstabilized alloys.
The Alloys 321 and 347 are particularly useful under conditions which cause polythionic acid stress corrosion of non-stabilized austenitic stainless steels, such as Alloy 304. Exposure of non-stabilized austenitic stainless steel to temperatures in the sensitizing range will cause the precipitation of chromium carbides at grain boundaries. On cooling to room temperature in a sulfide-containing environment, the sulfide (often hydrogen sulfide) reacts with moisture and oxygen to form polythionic acids which attack the sensitized grain boundaries. Under conditions of stress, intergranular cracks form. Polythionic acid SCC has occurred in oil refinery environments where sulfides are common. The stabilized Alloys 321 and 347 offer a solution to polythionic acid SCC by resisting sensitization during elevated temperature service. For optimum resistance, these alloys should be used in the thermally stabilized condition if service-related conditions may result in sensitization.
Pitting/Crevice Corrosion
The resistance of the stabilized Alloys 321 and
347 to pitting and crevice corrosion in the presence
of chloride ion is similar to that of Alloy 304
or 304L stainless steels because of similar chromium
content. Generally, 100 ppm chloride in aqueous
environments is considered to be the limit for
both the unstabilized and the stabilized alloys,
particularly if crevices are present. Higher levels
of chloride ion might cause crevice corrosion
and pitting. For more severe conditions of higher
chloride level, lower pH and/or higher temperatures,
alloys with molybdenum, such as Alloy 316, should
be considered. The stabilized Alloys 321 and 347
pass the 100 hour, 5 percent neutral salt spray
test (ASTM B117) with no rusting or staining of
samples. However, exposure of these alloys to
salt mists from the ocean would be expected to
cause pitting and crevice corrosion accompanied
by severe discoloration. The Alloys 321 and 347
are not recommended for exposure to marine environments.
Elevated Temperature Oxidation Resistance
Alloys 321 and 347 exhibit oxidation resistance comparable to the other 18-8 austenitic stainless steels. Specimens prepared from standard mill-finish production material were exposed in ambient laboratory air at elevated temperatures. Periodically, specimens were removed from the high temperature environment and weighed to determine the extent of scale formation. Test results are reported as a weight change in units of milligrams per square centimeter and reflect the average from a minimum of two different test specimens.
Weight Change (mg/cm2) | |||||
Exposure Time |
1300°F | 1350°F | 1400°F | 1450°F | 1500°F |
168 hours |
0.032 |
0.046 | 0.054 |
0.067 | 0.118 |
500 hours |
0.045 | 0.065 | 0.108 | 0.108 | 0.221 |
1,000 hours |
0.067 | -- | 0.166 | -- | 0.338 |
5,000 hours |
-- | -- | 0.443 | -- | -- |
Alloys 321 and 347 differ primarily by small alloying additions unrelated to factors affecting the oxidation resistance. Therefore, these results should be representative of both grades. However, since the rate of oxidation can be influenced by the exposure environment and factors intrinsic to specific product forms, these results should be interpreted only as a general indication of the oxidation resistance of these grades.
Physical Properties
The physical properties of Types 321 and 347 are quite similar and, for all practical purposes, may be considered to be the same. The values given in the table may be used to apply to both steels.
When properly annealed, the Alloys 321 and 347 stainless steels consist principally of austenite and carbides of titanium or columbium. Small amounts of ferrite may or may not be present in the microstructure. Small amounts of sigma phase may form during long time exposure in the 1000°F to 1500°F (593°C to 816°C) temperature range.
The stabilized Alloys 321 and 347 stainless steels are not hardenable by heat treatment.
The overall heat transfer coefficient of metals is determined by factors in addition to thermal conductivity of the metal. In most cases, film coefficients, scaling, and surface conditions are such that not more than 10 to 15% more surface area is required for stainless steels than for other metals having higher thermal conductivity. The ability of stainless steels to maintain clean surfaces often allows better heat transfer than other metals having higher thermal conductivity.
Magnetic Permeability
The stabilized Alloys 321 and 347 are generally
non-magnetic in the annealed condition with magnetic
permeability values typically less than 1.02 at
200H. Permeability values may vary with composition
and will increase with cold work. Permeability
of welds containing ferrite will be higher.
Typical Physical Properties | ||
Density | ||
Alloy | g/cm3 |
lb/in3 |
321 | 7.92 | 0.286 |
347 | 7.96 | 0.288 |
Modulus of Elasticity in Tension | |||
28 x 106 psi | |||
193 GPa | |||
Mean Coefficient of Linear Thermal Expansion | |||
Temperature Range | |||
°C | °F | cm/cm °C | in/in °F |
20-100 | 68 - 212 | 16.6 x 10-6 | 9.2 x 10-6 |
20 - 600 | 68 - 1112 | 18.9 x 10-6 | 10.5 x 10-6 |
20 - 1000 | 68 - 1832 | 20.5 x 10-6 | 11.4 x 10-6 |
Thermal Conductivity | |||
Temperature Range | |||
°C | °F | W/m•K | Btu•in/hr•ft2•°F |
20-100 | 68 - 212 | 16.3 | 112.5 |
20 - 500 | 68 - 932 | 21.4 | 14.7 |
Specific Heat | |||
Temperature Range | |||
°C | °F | J/kg K | Btu/lb•°F |
0-100 | 32 - 212 | 500 | 0.12 |
Electrical Resistivity | ||
Temperature Range | ||
°C | °F | microhm•cm |
20 | 68 | 72 |
100 | 213 | 78 |
200 | 392 | 86 |
400 | 752 | 100 |
600 | 1112 | 111 |
800 | 1472 | 121 |
900 | 1652 | 126 |
Melting Range | |
°C | °F |
1398 - 1446 | 2550 - 2635 |
Mechanical Properties
Room Temperature Tensile Properties
Minimum mechanical properties of the stabilized
Alloys 321 and 347 chromium-nickel grades in the
annealed condition (2000°F [1093°C], air
cooled) are shown in the table.
Elevated Temperature Tensile
Properties
Typical elevated temperature mechanical properties
for Alloys 321 and 347 sheet/strip are shown below.
Strength of these stabilized alloys is distinctly
higher than that of non-stabilized 304 alloys
at temperatures of 1000°F (538°C) and
above.
High carbon Alloys 321H and 347H (UNS32109 and S34700, respectively) have higher strength at temperatures above 1000°F (537°C). ASME maximum allowable design stress data for Alloy 347H reflects the higher strength of this grade in comparison to the lower carbon Alloy 347 grade. The Alloy 321H is not permitted for Section VIII applications and is limited to 800°F (427°C) use temperatures for Section III code applications.
Creep and Stress Rupture
Properties
Typical creep and stress rupture data for Alloys
321 and 347 stainless steels are shown in the
figures below. The elevated temperature creep
and stress rupture strengths of the stabilized
steels are higher than those of unstabilized Alloys
304 and 304L. These superior properties for the
321 and 347 alloys permit design of pressure-containing
components for elevated temperature service to
higher stress levels as recognized in the ASME
Boiler and Pressure Vessel Code.
Minimum Room Temperature Mechanical Properties Per ASTM A 240 and ASME SA-240 | |||
Alloy | Yield |
Ultimate Tensile Strength psi (MPa) |
Elongation |
321 | 30,000 (205) |
75,000 (515) |
40.0 |
347 | 30,000 (205) |
75,000 (515) |
40.0 |
Minimum Room Temperature Mechanical Properties Per ASTM A 240 and ASME SA-240 | |||
Alloy | Hardness, Maximum | ||
Plate | Sheet | Strip | |
321 |
217 |
95Rb | 95Rb |
347 | 201 Brinell |
92Rb | 92Rb |
Typical Elevated Temperature
Tensile Properties Alloy 321 (0.036 inch thick / 0.9 mm thick) |
||||
Test Temperature | Yield
Strength .2% Offset psi (MPa) |
Ultimate
Tensile Strength psi (MPa) |
% Elongation |
|
°F | °C | |||
68 | 20 | 31,400 (215) |
85,000 (590) |
55.0 |
400 | 204 | 23,500 (160) |
66,600 (455) |
38.0 |
800 | 427 | 19,380 (130) |
66,300 (455) |
32.0 |
1000 | 538 | 19,010 (130) |
64,400 (440) |
32.0 |
1200 | 649 | 19,000 (130) |
55,800 (380) |
28.0 |
1350 | 732 | 18,890 (130) |
41,500 (285) |
26.0 |
1500 | 816 | 17,200 (115) |
26,000 (180) |
45.0 |
Typical Elevated Temperature
Tensile Properties Alloy 347 (0.060 inch thick / 1.54 mm thick) |
||||
Test Temperature | Yield
Strength .2% Offset psi (MPa) |
Ultimate
Tensile Strength psi (MPa) |
% Elongation |
|
°F | °C | |||
68 | 20 | 36,500 |
93,250 (640) |
45.0 |
400 | 204 | 36,600 (250) |
73,570 (505) |
36.0 |
800 | 427 | 29,680 (205) |
69,500 (475) |
30.0 |
1000 | 538 | 27,400 (190) |
63,510 (435) |
27.0 |
1200 | 649 | 24,475 (165) |
52,300 (360) |
26.0 |
1350 | 732 | 22,800 (155) |
39,280 (270) |
40.0 |
1500 | 816 | 18,600 (125) |
26,400 (180) |
50.0 |
Impact Strength
Alloys 321 and 347 have excellent toughness at
room and sub-zero temperatures. In the following
table are Charpy V-notch impact values for annealed
Alloy 347 after holding the samples for one hour
at the indicated testing temperatures. Data for
Alloy 321 would be expected to be similar.
Impact Strength Alloys 321 and 347 | |||
Test Temperature | Charpy Impact Energy Absorbed | ||
°F | °C | Ft-lb | Joules |
75 | 24 | 90 | 122 |
-25 | -32 | 66 | 89 |
-80 | -62 | 57 | 78 |
Fatigue Strength
The fatigue strength of practically every metal
is affected by corrosive conditions, surface finish,
form, and mean stress. For this reason, no definite
values can be shown which would be representative
of the fatigue strength under all operating conditions.
The fatigue endurance limits of Alloys 321 and
347 are approximately 35% of their tensile strengths.
Fabrication
Welding
Austenitic stainless steels are considered to
be the most weldable of the high-alloy steels
and can be welded by all fusion and resistance
welding processes.
Two important considerations in producing weld joints in the austenitic stainless steels are (1) preservation of corrosion resistance and (2) avoidance of cracking.
It is important to maintain the level of stabilizing element present in Alloys 321 and 347 during welding. Alloy 321 is more prone to loss of titanium. Alloy 347 is more resistant to loss of columbium. Care needs to be exercised to avoid pickup of carbon from oils and other sources and nitrogen from air. Weld practices which include attention to cleanliness and good inert gas shielding are recommended for these stabilized grades as well as other non-stabilized austenitic alloys.
Weld metal with a fully austenitic structure is more susceptible to cracking during the welding operation. For this reason, Alloys 321 and 347 are designed to resolidify with a small amount of ferrite to minimize cracking susceptibility. Columbium stabilized stainless steels are more prone to hot cracking than titanium stabilized stainless steels.
Matching filler metals are available for welding Alloys 321 and 347 stabilized stainless steels. The Alloy 347 filler metal is sometimes used to weld the 321 alloy.
These stabilized alloys may be joined to other stainless steels or carbon steel. Alloy 309 (23% Cr-13.5% Ni) or nickel-base filler metals have been used for this purpose.
Heat Treatment
The annealing temperature range for Alloys 321 and 347 is 1800 to 2000°F (928 to 1093°C). While the primary purpose of annealing is to obtain softness and high ductility, these steels may also be stress relief annealed within the carbide precipitation range 800 to 1500°F (427 to 816°C), without any danger of subsequent intergranular corrosion. Relieving strains by annealing for only a few hours in the 800 to 1500°F (427 to 816°C) range will not cause any noticeable lowering in the general corrosion resistance, although prolonged heating within this range does tend to lower the general corrosion resistance to some extent. As emphasized, however, annealing in the 800 to 1500°F (427 to 816°C) temperature range does not result in a susceptibility to intergranular attack.
For maximum ductility, the higher annealing range of 1800 to 2000°F (928 to 1093°C) is recommended.
When fabricating chromium-nickel stainless steel into equipment requiring the maximum protection against carbide precipitation obtainable through use of a stabilized grade, it is essential to recognize that there is a difference between the stabilizing ability of columbium and titanium. For these reasons, the degree of stabilization and of resulting protection may be less pronounced when Alloy 321 is employed.
When maximum corrosion resistance is called for, it may be necessary with Alloy 321 to employ a corrective remedy which is known as a stabilizing anneal. It consists of heating to 1550 to 1650°F (843 to 899°C) for up to five hours depending on thickness. This range is above that within which chromium carbides are formed and is sufficiently high to cause dissociation and solution of any that may have been previously developed. Furthermore, it is the temperature at which titanium combines with carbon to form harmless titanium carbides. The result is that chromium is restored to solid solution and carbon is forced into combination with titanium as harmless carbides.
This additional treatment is required less often for the columbium-stabilized Alloy 347.
When heat treatments are done in an oxidizing atmosphere, the oxide should be removed after annealing in a descaling solution such as a mixture of nitric and hydrofluoric acids. These acids should be thoroughly rinsed off the surface after cleaning.
These alloys cannot be hardened by heat treatment.
Cleaning
Despite their corrosion resistance, stainless
steels need care in fabrication and during use
to maintain their surface appearance even under
normal conditions of service.
In welding, inert gas processes are used. Scale or slag that forms from welding processes is removed with a stainless steel wire brush. Carbon steel wire brushes will leave carbon steel particles in the surface which will eventually produce surface rusting. For more severe applications, welded areas should be treated with a descaling solution such as a mixture of nitric and hydrofluoric acids to remove the heat tint, and these acids should be subsequently washed off.
For material exposed to inland, light industrial, or milder service, minimum maintenance is required. Only sheltered areas need occasional washing with a stream of pressurized water. In heavy industrial areas, frequent washing is advisable to remove dirt deposits which might eventually cause corrosion and impair the surface appearance of the stainless steel.
Design can aid cleanability. Equipment with rounded corners, fillets, and absence of crevices facilitates cleaning as do smooth ground welds and polished surfaces.
Referenced data are typical and should not be construed as maximum or minimum values for specification or for final design. Data on any particular piece of material may vary from those shown herein.
NOTE: The information and data in this product data sheet are accurate to the best of our knowledge and belief, but are intended for informational purposes only, and may be revised at any time without notice. Applications suggested for the materials are described only to help readers make their own evaluations and decisions, and are neither guarantees nor to be construed as express or implied warranties of suitability for these or other applications.